最近は弊社製品「ジェイコア」としての販売よりもお客様独自の製品に搭載されるシステムの方が若干上回って参りました。製品は多岐にわたり、元となったジェイコアと同様に機上でツールを測定するものや関連して製品データをサ-バ上で管理し、諸元や保証書の発行や送付、あるいは製品自体の測定や良・不良判別、種別判定など画像ならではのニーズが高まっているように感じます。IT時代で、人手に頼らずラインを構築するのに画像関連技術は親和性が良いのと自己学習能力を付与できるのもメリットなのかと想います。
更にご要望は単純な測定ユニットに留まらず、専用サーバの構築や自動印刷・送付システム、付随して製品や材料の在庫管理、製造要求に対する各々の製造機の空き状況を管理するスケジューラーや稼働状況、製造進捗表示を含めたシステムなど枚挙に暇が無くなるぐらい広範囲に求められております。そういった意味合いでは市場において専業メーカーだけではニーズが無くなってきているのかもしれません。
それに伴って知見は画像処理だけでなくサーバ技術や関連する機器等の駆動知識、AIの開発など企業の財産とも言える保有技術の拡大は大変な反面、非常に有り難くもあります。言語一つとってもVB、C、C#、Python、PHP、JavaScript、Go、Kotlinなどお客様の環境に応じて求められますから順列組み合わせはほぼ無限です。(個人的にはPythonは方程式等が使えますので好きです。)
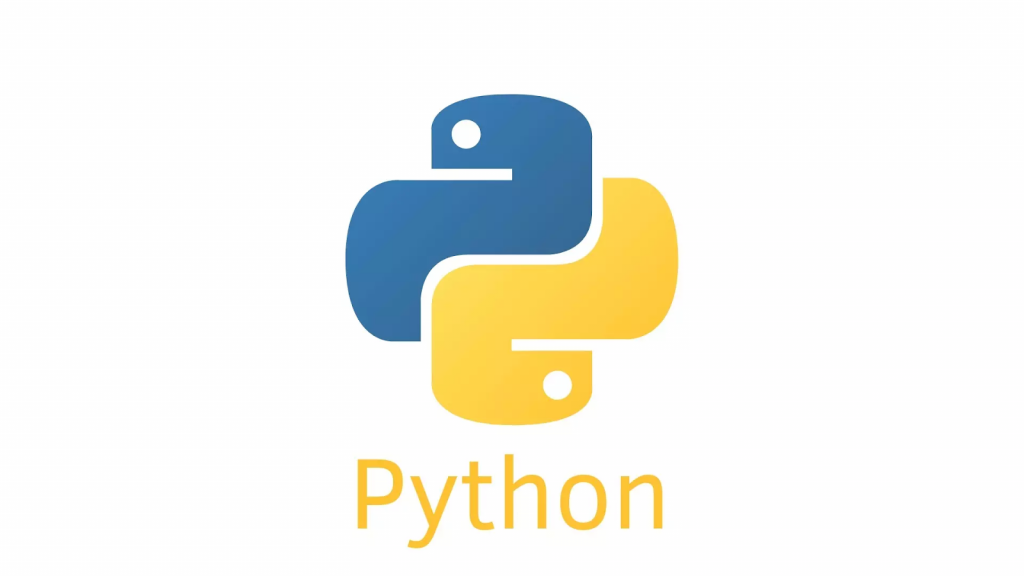
Pythonは、全世界で820万人のユーザーを持ち、ウェブ開発、機械学習、数学、データサイエンスなどの分野で幅広く利用されています。例えば、開発者はこの高水準言語を使用して、ウェブ・アプリケーションを設計し、大規模なデータセットを処理し、他のソフトウェアと組み合わせてワークフローを作成することができます。このオブジェクト指向プログラミング言語は、Mac、Windows、Linuxなど、すべての主要なプラットフォームと互換性があります。
プログラミング言語Pythonは、アクセスしやすく、分かりやすいように設計されています。Python言語は、英語と数学に似た構文を持ち、コード行数が少ないのが特徴です。Pythonのコードは通常すぐに実行できるため、開発者は同言語を使用してソフトウェアのプロトタイプを迅速に作成することができます。
今後も引き続き同様の開発を行って参りますが、もしもこのページを見てご興味が御座いましたらお気軽にご連絡賜れますと幸いです。日本発のOS、TRONも扱ってまいりますので様々な分野にお使いいただけると存じます。