マシニングセンターとATC
マシニングセンター(machining center:通称MC)は、それぞれの加工に必要な工具を自動で交換できる機能を備えており、一般社団法人日本工作機械工業会によると、以下のように定義されています。
中ぐり、フライス削り、穴あけ、ねじ立て、リーマ仕上げなど多種類の加工を連続で行えるNC工作機械で、それぞれの加工に必要な工具を自動で交換できる機能を備えています。
引用:『工作機械の種類と加工方法』一般社団法人日本工作機械工業会
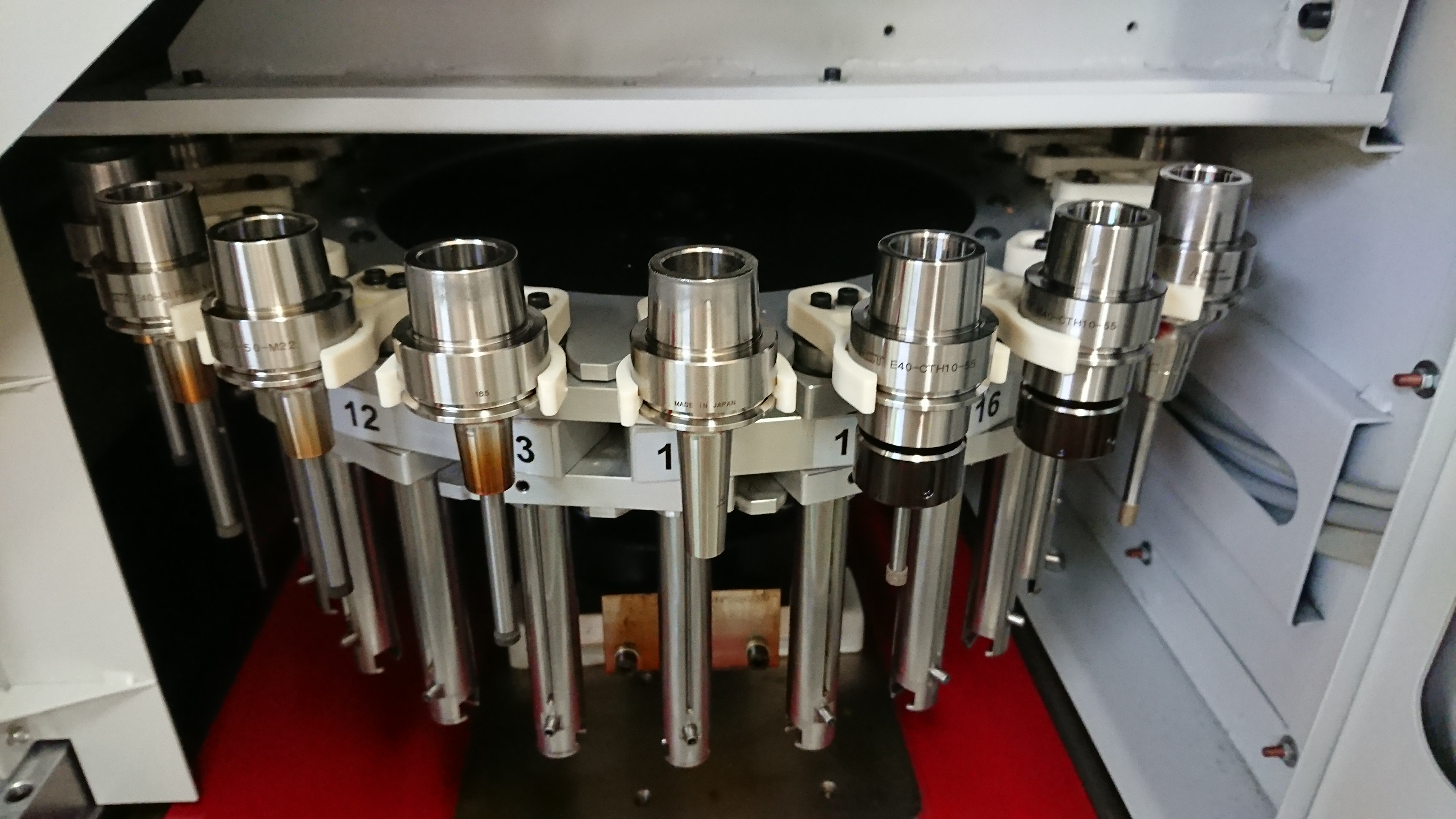
従いまして、ATC(Auto Tool Changer)が搭載されていない機械は厳密にはMCでは有りません。
勿論、中ぐり、フライス削り、穴あけ、ねじ立て、リーマ仕上げなど用途の異なる工具を交換しながら加工を行うこともありますが、一般的なのは大きな面積を切削する場合は比較的大きな工具、最小R指定がある場合や細かな造作の部分は小さな(あるいは細径)の工具を選択することではないかと考えます。
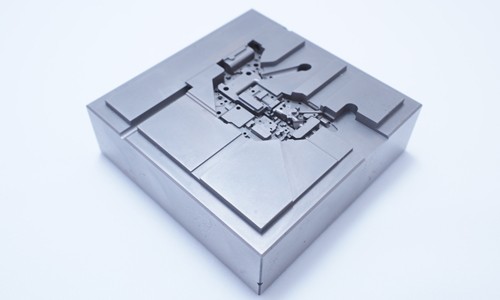
良い機会なので少々おさらいします。
大きな面積の部分は比較的大きめの工具で切削を行ったほうが、切削面積を大きく取れますので効率が良く、短時間で加工が終了します。一方で最小R指定などがありますと大きな工具では切削成形が出来ない、あるいは、細かな造作の部分は大きな工具では入らない等の事由で小さな工具で切削を行います。
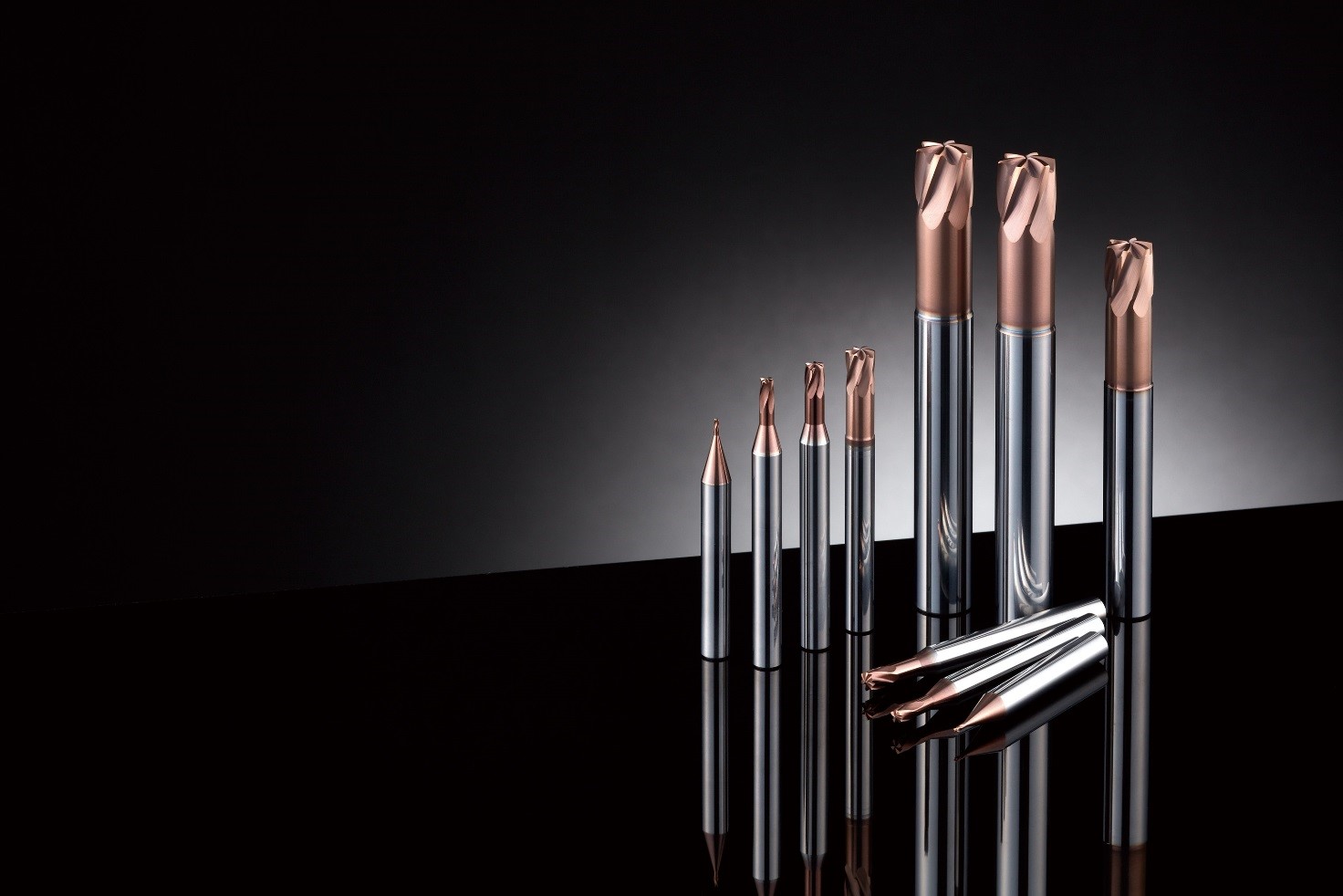
三菱日立ツール株式会社様の製品
しかし、工具径によって周速が異なりますので加工回転数は工具ごとに設定されるため、主軸の伸び量に変位が生じて結果として段差が発生します。多数の加工企業様で、これを嫌い使用される工具の中で一番細い工具で全加工を行うケースが見られます。
小さな(細い)工具で全加工を行いますと問題が2つ御座います。
1 加工時間がかかる
例えばΦ5mmの刃物で切削すべきところをΦ2mmで行った場合、理論上では2.5倍の加工時間になり
ます。回転数を上げて、送り速度も上げても一回の切り込み量が少なくなるために思うほどの効果は
上がらず、結果として加工時間がかかります。
2 摩耗による傾斜が発生する
小さな(細い)工具で全加工を行いますと工具の摩耗が無視できなくなります。特に大きな面積を持つ
製品の場合、時間により摩耗で切削量が変化するために傾斜が発生します。
MCにはATCが標準で付いておりますので積極的に使用する方向性がベストだと考えます。段差を恐れて利用しないのは少々、本末転倒ですね。段差が出ない対策をされれば、他方で中ぐり、フライス削り、穴あけ、ねじ立て、リーマ仕上げなど多種類の加工も安心して行えます。最終的に大きなコストダウンになります。