金型の内製化
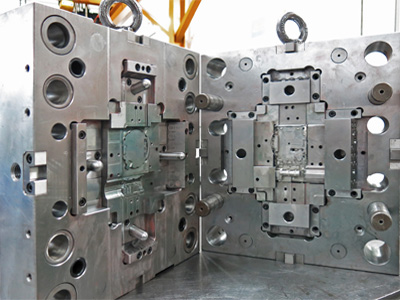
最近、1ヶ月ほど製品へのニーズ調査とお客様のご希望を承りに現場(工場)訪問をさせて頂いているのですが特に大手企業様においては金型の内製化がトレンドのようになっていると感じます。
一昔前は製品図が出図され、設計製作を外注さんが行うという流れが一般的であったように思います。内製化の波の要因を探るために、デメリットとメリットを考察してみます。
デメリット
1 設備
金型を製作するにはマシニングセンターから放電、研磨機等、多くの設備が必要です
ので、初期投資がかかる。
2 オペレーター
加工機械を稼働させるための人員を確保しなければなりません。設備と同様ですが、
仕事が有っても無くても固定費がかかりますのでリスクが有ります。
3 スペース
加工機械設置だけのスペースだけでなく、材料や仮置きの場所、オペレーターの居室
など製造に必要なスペース以外も必要になります。
メリット
1 技術力
金型に製造には多くの知見や技術を必要とします。継続させることでこれらの知見の
開発や技術力の維持を継続させることが出来ます。
2 企業独自のノウハウの保全
外部に図面等を出しませんので製品づくりのノウハウや知見が外部に流出する危険が
なくなります。特に際立った新製品や新技術の投入時には有利です。
3 納期
外注ではないために社内で納期の優先順位を元に工程を立てることが可能になります。
外注の混雑に工程を左右されることがなくなります。
4 手直し等
金型には設計変更や新製品への移行などが頻繁に発生しますが、社内であれば流用や
標準化など無駄のない設計と製作が可能になります。
デメリットとメリットを比較しますとある程度の製作量が担保できるなら内製化のメリットも大きくなるように思え、それらの損益分岐点は、どれだけ効率的に製造できるシステムであるかによって変わってきます。設備やスペースはともかくとして、オペレーターは最小であるほうがリスクは少なく済みます。
その視点で思い返しますと内製化を進められている企業様の製造システムは本当に最小の人員で製作が出来るように設計されており感心させられます。もっとも、弊社の製品(ジェイコア)絡みでお伺いしているので、そのような企業が多く見受けられることは否めませんが、ここ5年で間違いなくこの動きは活発になっております。先日拝見させて頂いた企業様ではマシニングセンター12台にオペレーターは2人でした。
専業の金型メーカーですと、様々なサイズや鋼材、業界に対応させるため加工機械もある程度、種類を保有しておかねばなりませんが、自社専用であれば、このあたりも統一が可能ですから有利に働くことも有るのでしょう。
今後も注目していたいと思います。